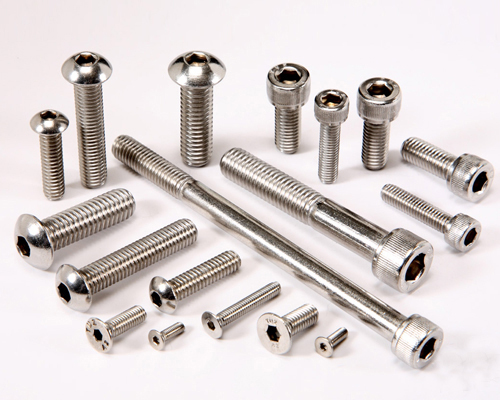
大家都知道,普通螺纹(包括各种公制、英制、美制、模数、径节螺纹)都是不能抗振防松的,加上弹簧垫圈也不行。原因就在于,普通螺纹实质上是不具有这方面的性能的,在其技术与产品的国家标准及国际标准上,都没有相关的性能规定与要求。
那么,有没有一种简单的方法,即就在原来的普通螺纹的基础上,稍作一些改进,就能使之“兼容”具有良好的防松抗振性能呢?答案是肯定的。
使螺纹实现抗振松防有很多方法,但有一个前提,就是不能破坏螺纹的牙型,原来是三角螺纹、梯形螺纹的,改进后内外螺纹还必须仍是其原来的结构,即不能一个是三角螺纹、梯形螺纹而另一是楔形螺纹(如现时市面上所说的“全金属螺母、‘XX牢’螺母”),也不能将一个传统螺纹变为二个螺纹(如开槽螺母、镶嵌尼龙的螺母等)。
其实,最简单的技术方案,就是我们通俗说的“径向过盈配合”的螺纹,或规范说法的“径向干涉螺纹”。螺纹径向干涉配合,可以是螺纹的大径干涉配合,也可以是其小径的干涉配合。当然,最简单的,是大径干涉配合的方案。
大径的干涉配合,也与普通机械零件一样,分基孔制和基轴制两种具体的实现方式。下面将详细向大家作介绍。
1.关于干涉(过盈)配合螺纹公差带的选择
对于一般的机械零件,孔与轴的干涉(过盈)配合,我们按照《GB1800 公差与配合》标准,选好相关的配合公差带就可以了。但干涉(过盈)配合的螺纹如何设计,我们不能找到相关的标准或资料介绍。国家标准《GB197 普通螺纹 公差》(2003年版)更规定,生产的螺纹,是不能超过其最大实体尺寸的,道理很简单,超过了最大实体尺寸,内外螺纹相互间是拧不进去的。
现时以名为“理想极限螺纹”技术生产的这种的干涉(过盈)螺纹副,却可比拟等效采用《GB1800 公差与配合》标准选择相关配合公差带。这套技术方案,适用于公制、英制、径节、模数等所有制式的螺纹。
2.选择干涉(过盈)螺纹副配合公差带的二个准则
一是配合基准:“径向干涉配合螺纹副”的配合基准建议选用螺纹的大径,一般优先选择“基孔制”。可以很形象地理解:外螺纹是轴,内螺纹是孔,如同“孔——轴”的配合一样。
二是径向干涉(过盈)量:考虑螺纹需重复装拆,且装拆时总会产生塑性变形的特点,“径向干涉配合螺纹副”干涉(过盈)量,应比普通“孔——轴”配合的要大一些。所以,选择的配合公差带,应高1-2级。
需定性与定量的考虑是:螺纹副配合时,螺纹大径的径向接触面积,远比“孔——轴”的少;重复装拆时,螺纹大径必然会产生一定的塑性变形;不同塑性的材料之间也存在明显差异;使用场合的不同(如强烈振动与高温)。某种特定螺纹副的最优配合公差带,需从实际应用的情况而定,要作一定的使用测试才能确定。对于配合要求与精度更高的螺纹副,其径向尺寸如需留磨削量或电镀,螺纹的大径径向尺寸,需同步作调整。
3.设计的一个技巧
设计生产径向干涉(过盈)配合螺纹的难点与创新点在于,这对螺纹副是如何自如地拧进拧出,又不会损伤螺纹牙型的。
由于这种“径向干涉配合螺纹副”,是一种大径配合的螺纹副,为使最初拧入的几牙用人手就能拧进去,我们只需将外螺纹前端几牙尺寸(我们称之为“导入段”)的外径,设计时选择负偏差就可以了,并以斜锥面过渡到正偏差的“配合段”。这就使干涉配合的螺纹副,其内外螺纹也可以很方便地导入拧进。
值得说明的是,要实现等效采用《GB1800 公差与配合》标准选择相关配合公差带,生产的这些内外螺纹,都必须使用到那种名为“高精度螺纹”的技术。具体的结构参数,暂不在本文讨论。
4.生产与检验
按“基孔制”生产的这种“径向干涉配合螺纹副”,外螺纹的牙型用专用的“高精度螺纹工具”进行成形加工,可只检验其外径公差。需更高精度的外径(大径),用外圆磨床进行加工,精度可达到IT4级以上。检验方法与检验外圆的外径一样;
内螺纹的牙型,用普通内螺纹工具进行加工,但必须检验其大径,用大径的“单项参数量规(包括通规与止规)”进行检验。该量规可自行生产,按传统孔量规的规程制造。
这种“径向干涉配合螺纹”生产的工艺、装备与成本,与生产传统螺纹、普通零件是一样的。
5.装拆、使用
这种“径向干涉配合螺纹副”,可以重复装拆、重复使用。它的干涉部分只是大径,并不是全个牙型的干涉,所以,正常装拆与使用,并不损伤螺纹牙型的主配合面(侧面)。
6.性能
这种“径向干涉配合螺纹副”最大的特征,是消除了内外螺纹间的径向间隙,具有极好的防松抗振性能;由于实现“全牙型高”承力,可比传统螺纹的“保证载荷”值高20%;它具有一定的自锁性能(还不能说是完全的自锁性能);它可以替代不能重复装拆的以“螺套”防松的螺纹副,成本减少一大半,性能也可靠得多。
同时以大径和小径实现干涉配合的“双径向干涉配合螺纹副”,可以具有密封性能。这是“非锥度配合密封螺纹”的一个情形。
7.可替代的市场
这种具有极好防松抗振性能,外表与传统螺纹一模一样的产品,在使用习惯上,大家也很容易接受。搓牙机,搓丝机出来的产品跟生产成本一样,但却新增了极好的抗振防松性能,它对传统螺纹的替代效应是十分明显的。包括生产这种抗振防松性能抽需的工具与量具在内的市场,每年将数以十亿元计。( 中轻网)线切割加工模具前的热处理实践 造成冷作模具损坏的因素很多,模具热处理工艺的好坏是提高模具使用寿命的一个关键因素,必须引起足够的重视。热处理工艺不合适,易使模具尺寸发生变化。冷作模具产生变形、开裂、硬度过高或过低、硬度不均匀等等,其根本原因是淬火或回火工艺不当。 根据多年生产实践证明,采用线切割加工冷作凸、凹模,加工后产生了变形甚至开裂,尤以碳素工具钢为甚。要解决这个问题,除选用合金钢以外,正确选择钢材牌号和掌握锻造工艺,制定正确的模具坯料热处理工艺是非常重要的措施。下面浅析线切割加工模具前的热处理实践。一些内型复杂的紧固件冷作模具,在线切割加工前,不仅要求硬度高、强度和韧性好,更重要的是要保证淬透性。在保证力学性能的前提下,要使模具淬火应力处于最低状态,更重要的是采取一些必要的措施。(1) 大、中型模坯在淬火加热前必须经过650℃预热0.5~1.5h,消除机械加工应力,减少材料由弹性畸变转变为塑性畸变的机会,增加模具的稳定性。(2) 尽量采用分级淬火或等温淬火工艺,使热应力和组织应力不同时产生。(3) 严格控制回火温度,要求测温精确,采用温度均匀的油浴炉或循环流动空气电阻炉为佳。淬火后,模坯需趁热回火,在保证硬度的前提下,尽量提高回火温度。趁热回火实质上是等温淬火,让模具内部形成不稳定的等温淬火马氏体的组织,然后进行二次回火,得到回火马氏体。对于大型模坯,截面较厚的模具有时必须进行第三次回火,最后加人工时效以保证模具的稳定性。(4) 各种模坯为减少变形量,可以对未加工的模具材料进行一次调质处理。在线切割加工前一般都应进行粗加工,然后进行淬火,以减少线切割加工余量以及线切割后的变形(5)大型模坯经锻造后需高温扩散退火或正火处理一次,再等温球化退火,消除网状碳化物,然后预先调质热处理,细化组织,减少应力。(6)对合金工具钢及截面较厚的冷作模具钢和H13、65Nb、GD钢材,淬火温度应提高20~30℃,以较大地提高淬透性、淬硬性和冲击韧度。(7) 对于型腔复杂、精度要求较高的模具,采用LD、Cr12MoV钢进行高淬高回二次硬化处理,再次中温回火就可以很好地消除淬火应力。(8)为了提高模具寿命进行的氮碳共渗,离子氮化或表面电火花熔渗等化学热处理,应在线切割加工后进行。化学热处理后,其表层的回火稳定性明显提高,为提高模具使用寿命创造了条件。对于淬透性差且尺寸既大又厚CrWMn钢及GCr15、9Mn2V钢的模具,由于淬不透会造成模具内应力很大,在线切割时及之后很容易产生较大的变形,甚至开裂。因而需采取预先开腔的办法。即淬火前在需要线切割处预1—2mm的线切割加工余量,经过淬火后再进行切割。预先开腔淬火具有刃口部分易淬硬的优点,且改变了内应力的分布状态。因此,不会产生变形和开裂,质量较优。需要了解更多的螺丝机械行业信息请关注石西阿福13560215171,或登陆官网www.shixi1980.com